The Basics: How To Choose The Right (Carbide Tipped) Saw Blade For Cutting Plastics
An observer viewing the development of cutting tools will note that the period immediately following WW II saw the beginning of a new era with the introduction of plastics, a radically different fabricating material, and the need for developing equally innovative tools to machine these new materials. Cutting plastic products successfully on a production basis presented a unique challenge due to the huge variety of the plastics developed and the widely differing reaction to the cutting process by each of the new plastic varieties. As saw blade manufacturers we have learned that in order to design and manufacture a successful cutting tool we must:
1. Understand as fully as possible the characteristics of each plastic variety, such as its relative hardness, sensitivity to heat, resistance to chipping and shattering, etc.
2. Design each blade series to suit the characteristics of each class of plastic material.
3. Manufacture the cutting tool to exacting tolerances with regard to plate flatness, allowable wobble and tension, grinding finish, diameter runout, tip clearances, bore specifications, etc.
Characteristics of Plastic Materials
The "Soft" Plastics
In general, plastic materials have been thought of as "Hard" or "Soft". Soft plastics, such as most nylon varieties, are severely heat sensitive, therefore the heat of friction developed during cutting must be minimized. This cooling effect is achieved by varying the number of saw blade teeth, (the more heat sensitive the plastic the fewer the number of teeth), by varying the tip geometry (more radial and/or tangential clearance and more tip overhang generate less friction), and by varying the kerf, (thinnest practical kerf produces less friction).
Ascending the hardness scale, but still considered 'soft' are the thermoplastic plastics, such as extruded acrylics, continuous cast acrylics and cell cast acrylics. As acrylics are moderately heat sensitive, blade design is directed toward reducing heat generation while maintaining smooth, chipless cutting. Design (and blade selection) decisions are influenced by
- The type of cutting equipment.
- Table saws.
- Vertical panel saws.
- Horizontal overhead cutting panel saws.
- Horizontal undercutting panel saws.
2. The thickness of plastic sheet.
3. The total stacked height of plastic sheet.
To illustrate how some of the above factors effect the correct choice of saw blade, let's follow an imaginary cutting room worker as he (or she) performs various cutting room jobs. A 1/8" thick 2' x 2' piece of cell cast acrylic is to be cut into 4" wide strips on a 10" table saw. A thin rim or thin kerf, 80 tooth blade with extra hard plastic cutting tips with 6° to 12° rake would be an ideal selection. Increasing the plastic thickness to 1/4" or 1/2" would alter the preferred selection to a 60 tooth blade since thicker plastic generates more heat. Fewer teeth reduce cutting friction. When changing to a larger or a full size plastic sheet while still cutting on a table saw the sawer must consider using a blade sufficiently thick and/or stable so as not to be deflected while the large plastic sheet is moved. The use of a stiffening collar is definitely suggested. Blade deflection during cutting will induce chipping, smearing from excess frictional heat, and possible tip or blade damage.
Rules of thumb for cutting clear plastics suggest:
- Use the maximum number of teeth to reduce or eliminate chipping but cut back on the number of teeth when smearing (overheating) begins to occur.
- Use a blade with the thinnest practical kerf.
- Use stiffening collars when possible.
- Keep your sawing machinery in tip top condition.
- Service your blades at the first signs of dulling.
- Always have a freshly reconditioned blade ready for emergencies.
Whether cutting on a table saw or using a horizontal or vertical panel machine, the suggestions outlined above generally apply. You will note however that machines built with overcutting saw carriages generally are fitted with low to negative rake angles whereas machines with underslung saw carriages carry blades with medium to high rake angles.
The "Hard" Plastics
The terms "soft" and "hard" when applied to plastics seems to date back to the early days of the development of plastics when the first commonly available plastic was the Thermosetting plastic called Bakelite. Thermosetting plastics were henceforth assumed "hard", whereas plastics created without need for added heat during manufacture, but readily bent using heat, such as the early thermoplastic product named Plexiglas® were called "soft" plastics.
Looking over the common plastics available today, with the exception of the phenolics and the Corin® class of plastics, most appear to be chemical groups of wide ranging hardness once considered as soft thermoplastics.
The Important Elements In Blade Selection
To select the right blade for your application you must realize how you expect the cut piece to appear. If speed of cutting is your prime objective then select a blade with few teeth, but don't expect a smooth chip free part. If you are looking for a fine, all round quality cut, with smooth surfaces and chip free edges then you must look further. The thickness, hardness and heat sensitivity of the plastic are your prime concerns.
Thickness |
The thinner the plastic the more easily it will chip, therefore the more teeth the blade will require, the lower the rake angle, the thinner the kerf and particularly with extremely soft or paper thin plastics, the probable need for sharp top bevel angles. |
Hardness |
The harder the plastic the more apt it is to chip when being cut. When experiencing chipping, increase the number of teeth per blade. However, should the material show signs of glazing or overheating, reduce the number of teeth. As stated previously, soft plastics require fewer teeth. |
Heat Sensitivity |
Heat sensitive plastics require fewer teeth, more radial clearance angle and more tooth overhang. |
And Don't Forget… |
The Saw Blade |
Many blade manufacturers specialize in the design and manufacture of blades specifically for the cutting of plastics. Most of these manufacturers have learned the importance of the careful selection of fabricating materials, the differences in blade design required for successfully cutting various plastics, and have acquired the latest. machines and techniques needed to produce and test their products. |
Catalogs |
Ask your blade supplier for their catalog featuring plastic cutting blade recommendations. |
The drawing below illustrates the key components of a circular saw blade.
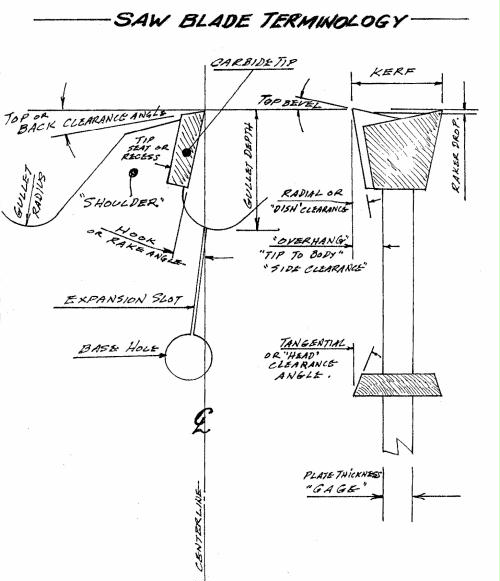
The following chart provides General Recommendations for circular saw blade selection:
BLADES FOR 10" TABLE MACHINES |
PLASTIC |
GENERAL RECOMMENDATIONS |
ACRYLIC, CAST |
Thin Rim 80 T |
Thin Kerf 80 T |
Std. Kerf 60 T |
ACRYLIC, EXTRUDED |
Thin Rim + Low Melt 80T |
Thin Kerf + Low Melt 80T |
Std Kerf + Low Melt 80/90 T |
COPOLYESTER |
Thin Rim + Low Melt 80 T |
Thin Kerf + Low Melt 80 T |
Std Kerf + Low Melt 80/90 T |
CORIAN ®, AVONITE®, Etc. |
Std. Plate + ATB 40-60T |
COROPLAST® |
Ultra Thin Kerf ATB Neg Hk. 96 T |
ENGRAVING STOCK |
Thin Rim + Low Melt 80T |
Thin Kerf + Low Melt 80T |
FOAM BOAR D |
Ultra Thin Kerf ATB Neg Hk. 96 T |
LEXAN® |
Thin Plate + Low Melt 80 T |
Thin Kerf + Low Melt + Neg Hk 90 T |
MIRROR POLYCARB |
Thin Kerf + Low Melt + Neg Hk 90 T |
NYLON |
Low Drag + Low Friction 24T |
P V C |
Thin Kerf + Low Melt 80 T |
Std. Kerf 60 T |
PHENOLIC |
Std. Kerf 60 T |
Std .Kerf 48 T |
Thin Kerf 90 T |
POLYCARBONATE |
Thin Kerf +Low Melt 80 T |
Thin Kerf + Low Melt + Neg Hk 90 T |
POLYETHYLENE |
Thin Kerf + Low Melt 80 T |
Std. Kerf 60 T |
POLYPROPYLENE |
Low Drag + Low Friction 24T |
POLYURETHANE |
Low Drag + Low Friction 24T |
SINTRA® |
Std. Kerf 60 T |
STYRENE |
Thin Kerf + Low Melt + Neg Hk 90 T |
UHMW-PE |
Thin Kerf + Low Melt 80 T |
Std Kerf + Low Melt 80 / 90 T |
VINYL, RIGID |
Thin Kerf + Low Melt + Neg Hk 90 T |
The "General Recommendations" chart pictured above is limited to 10" table machines but suggests the direction for selecting blades mounted on other type of machine. The table saw is merely a machine with a blade that power cuts from beneath the material. Isn't this the same situation found for Horizontal Panel Machines such as those made by Holzma, Gibben, Schelling, SCMI, Hendricks and many others? The difference is that the blade moves rather than the workpiece. The advantages lay in the ability of those machine to cut massive amounts of product automatically.
Horizontal Panel Machines with the blade mounted above the work table such as the popular but modest production Hendricks model climb cuts single plastic sheets. Table Saw recommendations are still your guide provided that the rake angles are changed to negative.
The cutting action of the typical medium size Vertical Panel Machine such as Safety Speed Cut, Holz-Her, Striebig, etc. is very similar to that of the Hendricks model discussed above. The blade is mounted above the plastic sheet and the blade spins into the plastic giving us the climb cut. These machines generally require a somewhat sturdier (thicker) blade to resist bending, especially during the horizontal cut. The need for negative hook still also prevails.
Machines such as Hendricks very large Vertical Panel Machine exhibits a truly remarkable cutting action enabling plastic stacks rather than merely single sheets to be cut. The saw blade starts its cut at the bottom of the machine scoring only the back sheet of the stack, proceeds to the top of the machine, automatically moves the blade forward to allow cutting the full stacked height, then cuts down to the bottom of the machine, completely severing the entire stack. The final downward cut is a typical Table Machine type action.
It should be noted that every Panel Machine requires constant vigilance and must be carefully and properly maintained. Attention to blade skewing is a continuing demand and adjustments must be made as quickly as possible.
We hope the discussion above has removed much of the mystery surrounding the selection of a blade for your particular plastic cutting application. Think about the plastic's characteristics, the quality you expect from your cut parts, the cutting machines available, and perhaps the hints offered in the chart. Not mentioned was the owner's or foreman's responsibility to train his workforce to improve their skills to produce to the best of their abilities.
Written by Bob Schultz and Roman Kordecki, General Saw Corporation, manufacturers of a full line of plastic cutting saw blades engineered to cut everything from acrylics to nylon and polypropylene.
For more information, contact Roman Kordecki at General Saw Corporation, 2518 Andalusia Blvd., Cape Coral, FL 33909-2903, 800-306-7297, Fax: 941-574-5328.
|