THERMOFORMING: Cut Sheet Pressure Forming A Look Into Thermoformings' High Pressure Forming
Pressure Forming
Pressure forming applications
have been rapidly increasing for
two main reasons. First, the
process can match the cosmetics
of injection molded parts and get
them to market quickly without
high mold costs and the long
lead-times associated with injection
molding. Second, the process
is being utilized to improve
and or upgrade parts that have
been traditionally vacuum-formed.
Pressure forming can
achieve better detail on the mold
surface of the sheet, hold closer
tolerances, have better material
distribution and less residual
stress when compared to standard
thermoforming.
Pressure forming enables designers to achieve high-end
products with sharp, crisp lines, zero radii and even zero
or negative draft angles. Engineers can include undercuts,
flanges, ribs and louvers in their
designs and still be assured that
the final products’ detail will be
kept. Pressure forming provides
aesthetic appearances, structural
integrity and more design flexibility
when solving part detail
dilemmas.
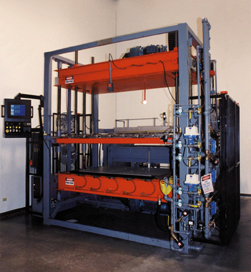
This process of thermoforming
typically uses female molds:
these molds can have multiple
textures, smooth areas and even
company logos all on the same
mold. If the final product requires
definition on the inside, the mold
would need to be male. For this
reason, converting designs from
other processes can be economically
advantageous.
Process Sequence
In this process, the sheet is heated to forming temperature,
the hot sheet is transferred to the forming station,
the upper mold (or pressure box) and lower mold are
brought together and compressed air is introduced
through the pressure box pushing the material against the
mold so more complex details of the mold are picked up
to achieve higher part definition (Figure 1).
Process Molds
Pressure forming molds are typically more expensive
than standard thermoforming molds for several reasons.
Pressure forming molds require a pressure box or second
mold half depending on the exact application. The mold
also needs to be water cooled aluminum in order to withstand
pressures and assure forming temperature of mold
surface. Due to these mold features and process sequence,
another advantage to pressure forming is introduced.
With the additional contact pressure of the forming
material with the mold surface the process allows more
control over cooling of the formed part resulting in less
stress and faster cooling times. Tooling deflection must
also be calculated to the amount of pressure that will be
applied, which can
increase mold pricing.
More intricate
products may require
molds with
articulating pieces.
Typical applications
include; automotive
panels, computer
housings and
bezels, cases, medical
housings, exercise
equipment, instrument
panels,
light lenses, television
backs, appliances,
aircraft interiors
and many more.
Process Materials
Generally speaking, all materials which can be thermoformed
can be pressure formed. However, as might be
expected, some are more suitable than others. Amorphous
polymers such as ABS, Polystyrene and acrylic are
ideal for both thermoforming and pressure forming in giving
high viscosity melts over a broad temperature range.
Polymers having a mixture of crystalline and amorphous
characteristics such as polypropylene and polyethylene
are intermediate in performance but are being molded
successfully. A further
consideration is that
certain materials, such
as polycarbonate, are
highly hydroscopic and
must be thoroughly
dried before thermoforming.
This is not
necessarily a problem
but it does add to the
expense of processing
the material.
Given the wide range
of materials that can
be pressure formed,
normal plastic design
criteria apply. The
material selected must
fulfill the specific requirements
of the part in terms of aesthetics, fitness for
purpose and compatibility with its expected environment.
Last but not least, the part must also meet economic
goals.
Types Of Pressure Forming:
Air-Assist Pressure Forming
Air-Assist pressure forming is referred to as pressure
forming without locking the platens. Air assist pressure forming is defined as the amount of detail in a part that 30 psi will
create (using 16 psi from air pressure in addition to 14 psi from
vacuum {29hg}). This is typically only done on machines with
hydraulic or motor driven platen drives. Without locking the
platens, machines are only designed to hold the amount of pressure
created by the cylinder or brake-motor before the tools separate,
releasing the air pressure.
High Pressure Forming Platen
Lock-Up Pressure Forming
Air cell lock up, high pressure forming is done with machinery
specifically designed for this process. This technique extends both
platens, locking them to each other then inflating air cells under a
floating plate which can be attached to either the
bottom or top platen. This method provides the
force necessary to create a high pressure seal.
High pressure forming is the amount of detail in a
part that 60 psi will create using 50 psi from air
pressure and 10 psi from vacuum. Common pressures
are 35 psi to 60 psi, however in some applications
utilizing large parts or highly engineered/
reinforced materials, higher pressures
may be required.
Compression Forming
Compression forming is the thermoforming
process utilized for creating high detail on two
sided parts, achieving an exact finished gauge and
creating a high pressure knit between two mold
surfaces (twin sheet forming). Most applications
require locking platens. This is determined by
sheet gauge and material type. In single sheet
forming, the part will be formed by the bottom
tool compressing the material against the top
tool. This requires matched tools.
Pressure Forming VS Injection Molding
The pressure forming market is continually
increasing from year to year and does hold several
advantages over injection molding.
Tooling can be up to 80% less for upfront tooling
expenses on pressure forming versus injection
molding. The significant savings comes from pressure
forming molds only needing to be machined
aluminum or cast aluminum, rather than
machined steel. Also, most pressure forming
molds only require one mold half and a pressure
box instead of two matched molds that are
required in injection molding.
Costs are usually much less due to tool amortization,
especially when comparing limited production
quantities. These advantages become even
more significant as the size of the parts become
progressively larger. Lead times and deliveries
are much faster, with lower prototyping costs,
therefore allowing for more time on final design
modifications. With quicker prototyping capabilities,
pressure formers can ensure maximum flexibility
and even visibility of the product definition
before finalized. Pressure forming can also eliminate
negative conditions that are common to the
injection molding process; such as ejection marks,
gate marks and porosity.
Written by Michael P. Alongi, Sales Director for MAAC Machinery Corp., manufacturers of a wide range of cut-sheet thermoforming machinery.
For more information, contact MAAC Machinery
Corp., 590 Tower Blvd., Carol Stream, IL 60188,
630-665-1700, Fax: 630-665-7799, E-mail:
sales@maacmachinery.com, Web: www. maac-machinery.
com.
|