THERMOFORMING: Thermoforming Molds
From epoxy tools on
single stations to
water-cooled aluminum
tools on three station
rotaries and four station
twin sheet pressure
formers, cut-sheet
thermo-formers
require a wide
variety
of molds for the parts
and products they produce.
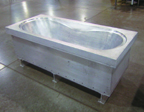
There is no standard type
of material from which
molds are manufactured.
With low pressure and/or
low volume applications,
wood or epoxy molds may
be acceptable, whereas
with high pressure and/or
high production applications,
cast or machined aluminum
molds with temperature controls
would usually render
the best performance.
Before forming a new part,
the thermoformer must consider
several criteria in order
to determine which mold
material is best for the job.
What type of plastic material
will be formed? What
forming technique will best
suit the product? Will it
require a male or female
mold? What is the amount
of production required
from the mold? Is the
finished product too
complex for simple
mold materials? Does
the overall part size
justify an expensive
mold material or does
the parts configuration
change from year to
year? These are just a
few of the factors to
consider before
determining which type
of mold material to utilize.In addition to selecting the best material, thermoformers
must then determine shrinkage rates for the different
types of thermoplastic materials they will be forming.
They must also determine whether or not the mold must
be temperature controlled, or even multi-zoned temperature
controlled.
Cut-sheet thermoforming machinery suppliers should work
with the thermoformer to develop and design their
machinery and/or sequencing of their machinery based on
a customer’s specific mold and its characteristics.
With the machinery manufacturer involved, cycle times
(parts per hour) can be guaranteed, along with a proven
timed forming sequence
and a finished
product that meets the
specification. This is
usually accomplished
concurrent within the
machinery build time.
Machine, mold and
part approval can then
be done concurrently at
the machinery manufacturer
at time of training.
This has become
more and more popular
with clients because it
eliminates the very
costly and very timely learning curves that come with new
machinery, new tooling, new material and new sequencing.
Written by Michael P. Alongi, Sales Director for MAAC
Machinery Corp., manufacturers of a wide range of cut-sheet
thermoforming machinery.
For more information, contact MAAC Machinery Corp., 590
Tower Blvd., Carol Stream, IL 60188, 630-665-1700,
Fax: 630-665-7799, E-mail: sales@maacmachinery.com,
Web: www.maacmachinery.com.
Pictures provided by: Thermoform Tooling Works Carol Stream, IL
|