Thermoformable Nylon and Acetal
The perennial question “what’s new?” in nylons and acetals is being met this year by the introduction of a new grade of each material that is opening new and significant markets.
Nylon
In February of 2003, Penn Fibre Plastics announced commercial availability of Pennite 4508, a thermoformable, type 6, glass filled nylon. As nylons have long prospered in the injection molded and fabrication markets, Pennite 4508 is the first of several new nylons being developed with the thermoforming industry in mind. The expansion of nylon into the $6 billion U.S. thermoforming industry has been rapid and is expected to well exceed industry growth projections.
Pennite 4508 is a high viscosity, impact modified, heat-ageing stabilized nylon with the high melt strength required for the thermoforming process. The continuous service temperature of 140°C/ 284°F and the peak operating temperature of 170°C/338°F make Pennite 4508 a prime choice for under-the-hood applications in ducts, shrouds and covers. The enhanced mechanical strength of the material allows it to be considered in large, thin wall design applications that often prove problematic for injection molders. The material is black for service operations.
The material was first validated as thermoformable by Adolf Illig Maschinenbau GmbH & Co. in Heilbronn, Germany. Illig is a leader in the design and production of thermoforming equipment in Europe. Further testing of Pennite 4508 has been performed by Freetech Plastics, Inc., a uniquely innovative thermoformer, located in Fremont, CA. After successfully molding the material in a sequence of trials, Freetech Plastics applied their design expertise and twin sheet molding technology to develop an air damn for an automotive under-the-hood application.
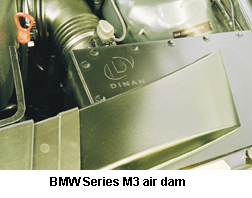
Pennite 4508 is available in coils from .010” to .093” thick and in sheet form from .031” to .250” thick in widths up to 48”. Metric sizes for the international markets go up to 1250mm in width. New variations of the material to be released shortly will include a type 6 impact modified grade (no filler) and two grades of type 6/6 nylon in 15% and 25% glass filled.
The enhanced mechanical properties and extended heat range of Pennite 4508 also make it a very attractive material for stock shapes fabrication applications. Distribution of the stock shapes products is facilitated through the Ensinger/ Hyde distribution network. Acetal
If you have watched the materials market news closely you are already aware of a new acetal development from DuPont Engineering Polymers. This new material, Delrin® FS, is the worlds first thermoformable acetal. The development of this material by the DuPont™ Delrin Forming Solutions group began last year with Penn Fibre Plastics in their Greenwood, DE manufacturing facility. The introduction of the material to the thermo-forming industry has been extremely well received for the same type of applications that Delrin has been associated with traditionally. Products that require chemical resistance, high strength ratios, scratch resistant finishes and the other properties typically associated with Delrin, may now be thermoformed with Delrin FS. Major markets for this new material include medical, electronics, automotive, packaging and industrial applications. Delrin FS is expected to become a staple in the thermoforming industry just as other Delrin formulations have within the stock shapes and injection molding segments of the industry.
Delrin FS is available in natural (white) and a wide range of stock and custom colors. Coil products are available from .010” thick to .093” thick in master coils up to 24” wide and may be custom slit to widths as narrow as .250”. Sheet products are available from .031” to .250” thick in standard and custom sizes up to 48” wide. Metric sized sheets for the international markets are available up to 1250mm wide.
The first thermoforming trials of Delrin FS were performed by Freetech Plastics. Freetech validated the formability of the material in several molds with varying geometry and concluded that the sheet material not only made an excellent looking product but that it also was very consistent with respect to processing parameters. The design team at Freetech is presently engaged in developing several products for this new material.
Secondary validation of the formability of Delrin FS has also been performed by Adolf Illig, GmbH & Co. at their labs in Heilbronn, Germany with representatives of the DuPont Delrin Forming Solutions team and Ensinger, GmbH, the parent company of Penn Fibre Plastics. Once again, the ease of processing and fine replication of detail impressed all present.
In addition to the thermoformable characteristics of the new material, Delrin FS also brings some new and unique properties to the market. This new material is the most versatile acetal ever available when it comes to topographical decorations and printing. Most printing and decorating processes, including sublimation printing, is achievable. Bonding applications are greatly enhanced and adhesive applications may be even further advanced with the addition of fiber backing materials. As two of the industries largest materials enter new markets they are sure to provide the rising tide that will float all boats. These mainstays of the industry will surely carry more materials in their wake and open opportunities in the world of thermoforming.
The distributor’s direct access to these materials will allow them to serve an industry with an estimated 1,000 processors in North America. Fabricators will find multiple opportunities to partner with thermoformers for hybrid products that may be formed and then finished with conventional fabrication techniques. End customers for nylon and acetal applications will benefit from an expand-ed choice of processes to meet their varying product demands and the plastics industry in general will reap the reward of higher volumes on the two largest families of engineering materials.
For more information, contact Dave Pincin, Operating Manager, Penn Fibre Plastics & Co., Inc., 2434 Bristol Road, Bensalem, PA 19020, 215-702-9551, Fax: 215-702-9552, E-mail: davidp@pennfibre.com, Web: www.pennfibre.com.
|