Lasers Improve Sign & Display Fabrication
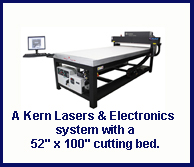
Lasers offer attractive advantages for cutting acrylic
and other plastics used in signage and point-of-purchase
displays. Recent advances in technology have
rendered laser systems more cost-effective than ever,
making them increasingly accessible to even small fabricators.
This article reviews the current generation of laser
systems and the applications that they service.
Laser Cutting Basics
Most acrylic cutting in the sign industry today is still
performed with the mechanical router. Probably the most
significant disadvantage of this method is the fact that
router cutting produces a rough edge, which must then be
subsequently flame polished in order
to give it a smooth, transparent
appearance. For some applications,
additional limitations of the router are
its inability to produce sharp corners
and render intricate detail.
The laser is a non-contact tool that
cuts by essentially melting and vaporizing
away material. Typically, plastics
cutting is performed using the carbon
dioxide (CO2) laser because its
infrared output is strongly absorbed
by most organic materials, even those
which appear transparent in the visible
spectrum.
Laser cutting offers several advantages
over the router. First, laser processing
can deliver a variety of cut
edge finishes, including a smooth,
transparent edge which entirely eliminates
the time and cost of flame polishing.
Next, the focused laser beam
produces a very narrow cut width (as
small as 0.005 inches), thus enabling
the production of very sharp edges
and angles, as well as the ability to
render very fine features. The laser is
also a flexible tool which can perform
anything from kiss cutting to through
cutting, with very accurate control of
cut depth and high repeatability and
consistency, without the need to change tools.
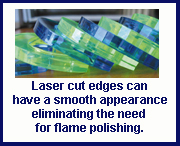
Furthermore, laser cutting can be employed on materials
over a wide range of thicknesses, from mylar sheets to
1.25 inch acrylic.
Practical Laser Systems
The typical laser system has a cutting bed, ranging in
size from 2' x 2' to 6' x 10', onto which the material is
placed. The laser beam then travels over its surface, under
automated control, to perform the cutting.
Utilizing a laser cutter is usually quite straightforward.
For example, all the systems supplied by Kern Electronics
& Lasers connect to a computer via a USB cable, and appear as just another printer application. Kern has configured
their printer driver to enable simple drawings, produced
in applications such as CorelDraw or Adobe
Illustrator, to easily yield both simple cuts and complex
results. For instance, hairlines in the drawing tell the system
to cut; but, nine different cut depths are supported
through color coding of the lines. Engraving of graphics,
letters and logos is supported by simple grayscale fills
inside shapes. A white fill produces the shallowest result,
while black delivers the deepest engraving. Gradient fills
enable accurate reproduction of sophisticated and complex
graphics.
Recent advances in CO2 laser technology have been key
in reducing the cost and improving the capabilities of
these systems. In particular, the development of sealed,
slab discharge CO2 lasers, such as the Diamond series
from Coherent, offer better performance and practical
characteristics than older laser designs. Specifically, these
slab discharge lasers are now much more compact (for a
given output power) and more reliable than their predecessors.
Furthermore, the high stability and favorable output
beam characteristics (piercing power) of slab discharge
lasers enable them to cut thicker materials and
deliver superior edge quality. All this allows a 400W slab
discharge laser to deliver the cutting speed and capability
of a much more powerful and therefore more costly
laser, thus lowering purchase price and long-term cost of
ownership.
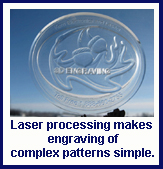
Typical Applications
One common signage application is cutting out letters
or other shapes from acrylic sheets, typically varying from
1/8 to 1 1/4 inches in thickness. These are then affixed
using adhesive to a signboard. The individual cut pieces
can vary is size from a fraction of an inch to several feet in
dimension.
The appearance of the laser cut edge varies depending
upon the cut speed. At lower speeds (typically in the 30 inches/
minute range) the laser beam produces an edge that has
the same appearance as a flame polished part, while at higher
speeds the cut surface looks frosted or milky. Typically,
acrylic lettering is produced with a smooth surface. Also, a
new trend in this area is to light the sign with LEDs, which
requires good control over edge quality for proper results.
Another popular sign making technique benefits from
the laser’s ability to remove thin layers of material with
high precision. Here, the laser is used to cut a shape from
a piece of acrylic that is already painted on one side. Then
the laser etches only the paint from the rear surface in the
areas in which characters and graphics are to appear.
Next the back surface is painted with a contrasting color
to make the etched areas highly visible.
The laser also excels at engraving complex, 3D patterns.
Again, these are supplied as a grayscale coded
graphic to the system. In this case, the laser raster scans
across the
part to produce
the
engraved
pattern, and
then cuts the
outside
shape of the
piece using
vector scanning.
Typically, the
engraving is
done at a
speed that
produces a
lightly frosted appearance.
The same laser system that cuts 1-inch thick acrylic
sheets can also be used to cut very thin mylar for stencils.
These are then used for sign painting.
In conclusion, laser systems enable even relatively
small sign making operations to access a range of
sophisticated processing capabilities. They can reduce
product turnaround time, deliver greater added value to
customers, and hence increase profitability for sign manufacturers.
Written by Derek Kern, VP of Sales & Marketing, Kern
Electronics & Lasers, and Andrew Held, Ph.D., Product
Marketing Manager, CO2 Lasers, Coherent. Kern Lasers
has been a leading manufacturer of state-of-the-art laser
cutting and engraving systems since 1982. All Kern laser
systems are designed to handle a demanding production
schedule.
|