PLASTIC WELDING: Repairs on Plastic Parts
This article will discuss the proper repair of broken plastic items. Almost everyone has had an experience with a broken plastic part such as industrial equipment, a child’s toy, lawn furniture, automobile parts, etc. Plastic as we know it and use it has a limited lifetime. The life span may be longer or shorter depending on the environmental conditions the parts are used in. Cold weather, improper protection from UV rays, and chemical contamination all have a specific effect on the plastic part and its life. These are circumstances that are not easy to change or control. Damage also can occur that is mechanical in nature. For example, a hard impact on a water tank or car bumper can break the plastic. Sometimes the broken parts are not worth replacing with new ones or a damaged piece would be difficult to replace because it is ‘built-in’ to a complex system. An alternative could be to repair it.
From my previous articles, you should know that some thought is required before you start welding or splicing in order to make a good repair. The key factor is to know the material. There are several different ways to determine which type of plastic you are working with (see Nov/Dec 2000 "The Right Start"). The material will impact the repair process and method you choose. Thermoplastic and thermoset materials are totally different and as mentioned in earlier issues, thermosets are not weldable, while most types of thermoplastics are. This leads to different types of repair. Because the basis of this series is plastic welding I will spend more time on thermoplastics than thermosets.
Thermosets can be fixed by using Phenolics or Epoxies. To achieve more strength at the repaired area, fiberglass or carbon fibers are used. This mainly enforces the repaired area.
Now, let’s take a closer look at thermoplastics and how to make a quality repair on these materials. To start, you must determine the type of plastic that requires the repair. This is the most important step because if you use a different welding rod material than the broken plastic material, they will not bond together. You will also find that certain thermoplastic groups called "Polyolefines" exhibit a very low surface energy. This also makes it very hard to bond them with an adhesive or glue. To put it simply, nothing will stick to them. Some suppliers offer polyolefine adhesives that will produce a chemical reaction and increase the surface energy. My observation is that this will only work for a limited period of time. As a permanent solution I would not recommend it. From my experience, a proper weld on these materials would be more appropriate, however, try the adhesive yourself to see what works best for you. Other types of thermoplastic materials are perfect for using adhesives on (May/Jun 2001 "Splicing of Thermoplastic Materials"). Please feel free to contact me if you are unsure of a certain material.
If you choose welding as a solution to make the repair, the welding rod needs to match the piece that is damaged. Keep in mind that I am not talking about the color. Color does not indicate the type of plastic material. The material itself needs to match. With a little luck there is a stamp located somewhere on the part that identifies the plastic material.
Normally you will find that two different kinds of repair are most common. One type of repair is a crack repair and the other type is when pieces of the broken part are missing.
Let’s start with the crack repair first. Fractures happen when the plastic unit shows stress inside the material. Stress occurs for many reasons from the manufacturing process to the storage, handling or even the use of the piece. So to prevent the crack from traveling further through the material, drill a slightly larger hole than the fracture itself at the ends of all cracks. A diameter of 2 mm or 0.08" would be appropriate. The round shape of the drilled hole will distribute the stress more evenly and will help to stop further cracking. If the fracture runs the whole length of the plastic part, a bigger gap appears. This is another sign of stress development inside the plastic. In order to bring the parts together, new stress might emerge, so handle these areas with care.
"V" grooving the breakage ensures better weld strength because of the increased welding zone which allows the filler material (welding rod) to fill the gap much more effectively. The best tool to do this kind of preparation is a stick scraper with a right angle on it. Angles of 80º to 90º for an injection welder and 60º to 70º for hot-air units are suitable. After this preparation is complete, tack or clamp the parts into the proper position. The welding rod has to be clean for the same reason the surface needs to be cleaned. Oxidation, dust, grease and other contamination reduces the weld strength substantially. Use a blade scraper to do this type of preparation properly.
Another critical part is the weld temperature. I often hear the following expression from attendees in my plastic welding seminars in Edmonton (please contact me if you are interested in attending a one-day-seminar): ‘I can weld much faster when I crank up the temperature. This makes it more efficient’. This might be correct, but are they thinking about what happens inside the material? I know that I repeat myself over and over again regarding this point, but it is important to know that thermoplastics have a certain weld temperature range. Too hot or too cold is not good for the quality of the weld. Turning up the temperature above the maximum weld temperature will damage the molecular structure of the plastic. A mixture between the molecules will not be possible anymore because the material has been destroyed. If the temperature is too low, the welding rod and the parent material cannot mix probably. Even though it might stick, we don’t want to call this "a weld". Knowing the material and its properties is a major concern. This is limited to not only repairs, but to all plastic work-ups.
To fill the prepared crack, the pressure on the welding rod is very critical. The molecules cannot mix if the pressure is too high or too low; therefore some practice is necessary. After completing the weld, do not leave the area as is. Smoothing down the weld bead to the surface of the part will avoid new cracking areas. When possible, weld the damaged section from both sides. This takes a bit longer, but will increase the quality of the repair enormously.
Use the same process for the repair of a plastic part where some pieces are missing. The areas where pieces are missing normally show irregular shapes. Usually it is easier to cut out the complete damaged area in a shape that is round, square or rectangular. Square and rectangular shapes need to have rounded corners in order to make them easier to weld. A good fit of the replacement piece makes the repair process simpler, quicker and stronger. A matching material thickness will avoid weak spots in the repair as well. The replacement parts can be cut out of sheets or pipes or other damaged parts. The important criteria being that the material, the thickness and the shape will fit the missing area.
The right welding equipment can make a big difference in the quality and appearance of the repaired section. The most common equipment to perform plastic repairs with is hot air welders and injection welders. Hot air units are usually less expensive, however, their use requires quite some skill to make a strong weld. As always, the right preparation and the right pressure on the welding rod are important.
On thermoformed (vacuum formed, press formed) parts, problems might occur when the heated air hits the surface and starts spreading out in all directions. It is very difficult to control this airflow. Thermoformed pieces have a high amount of stress in the formed areas. When the hot air reaches these spots, it might burn a hole in the section or a deformation might occur. This is where the advantage of an injection welder comes into play. These units use a heated aluminum tip instead of hot air to melt the parent material. The heat is very located in the area where the tip touches the weld area. Deforming or holes will not occur as easily and the quality of the weld will show a higher strength.
The drawings below illustrate a typical crack (top) and missing part (bottom) repair.
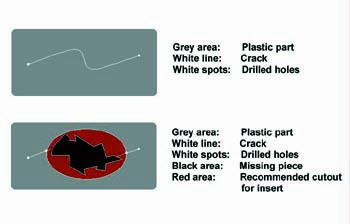
If you have any questions regarding this article, please contact me and I will try to help. I would also be glad to provide more information on the One-Day-Plastic-Welding-Seminar.
If this or any of my previous articles help you to understand the important aspects of plastic welding and all the considerations that have to be made, my goal has been achieved.
Past articles in this series can be viewed by clicking on the links above.
For more information, click on the Author Biography link at the top of this page.
|